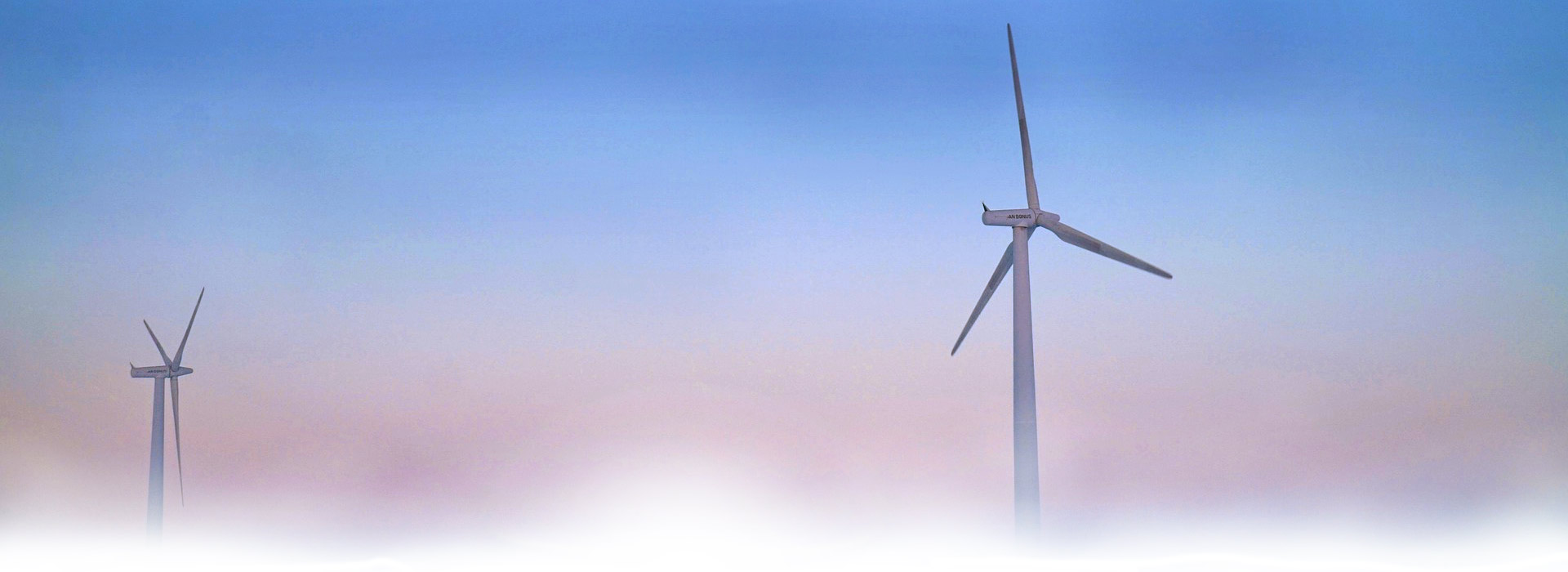
Your Questions
and our responses
Can ACT support the entire development process, from the aerodynamic design to prototype production of rotor blades?
Yes, we offer services for the complete value chain of rotor blades.
One of ACT’s philosophies is "Design for Production”. We support our customers further with design of moulds and tools, with the installation and adjustments of production equipment, in training of process engineers and prototype manufacturing.
Does ACT have its own family of aerodynamic profiles and reference projects?
In order to achieve optimum energy yield, the aerodynamic profiles are developed specifically for rotor blades. In most cases, existing and tried-and-tested profiles will be modified, but sometimes we need to develop new profiles. Special features such as Vortex Generators, Gurney Flaps, Boundary Layer Fence or Serations can be used according to the requirements of customers. ACT and its partners can draw on several tried-and-tested profile series with references. If necessary, rotor blade aerodynamicists and research facilities will be integrated into the design process.
We want to shorten the cycle times for manufacturing rotor blade. Can ACT help us?
Yes. ACT has substantial experience in cycle time reduction.
ACT provides support for production management, work organization, material flow, process optimization and training on the shop floor.
Together with customers, ACT at first monitors and analyzes the production in order to identify improvement potentials, to define goals and responsibilities, and to create a comprehensive work plan.
During implementation, it is particularly important to monitor the progresses and optimize the quality through observations and statistical analysis. As a rule of thumb, cycle times in the "Green Body Production" are to be reduced from 48 hours to 40, 32, 28 and then to less than 24 hours.
The duration of a cycle time reduction project depends on the initial situation in the factory. Usually it takes 4 to 6 months.
Can ACT help us optimize the curing time?
Yes. ACT has developed an own tool to optimze the curing time.
With ACT self-developed tool, we can calculate the glass transition temperture (Tg) and the real temperature within a laminate, get curing time on point and avoid hot spots.
Our tool considers different layups (monolithic/sandwich), the insulation cover on top of the layup as well as removal of the insulation cover, manufacturing hall conditions (in summer or in winter), and the heat-up and cool-down behaviors of moulds. Accordingly, we can design the best strategy to control the heating system and insulation as to optimize the curing process.
We also can use this technique for the curing of the blade bond.
How can we reduce the production cost of rotor blades?
In general, the production cost can be reduced by
(1) having robust, simple and fault-tolerant production processes,
(2) optimizing production organization, workflow and material flow (adapted to the blade output), and
(3) reducing production wastes and manufacturing materials.
If the demand for rotor blades is high, a "green body" production within 24 hours can be extremely cost-efficient.
We are concerned about potential defects in carbon fiber spar caps. What are ACT’s suggestions?
Non-visible, internal defects in carbon spar caps are often critical. ACT has experience in detecting these defects.
In addition, ACT has established failure criterions regarding the waves in carbon spar caps. We distinguish among tolerable waves, critical waves which need extra clearance from R&D, and non-tolerable waves. Our failure criterions have been adopted and proved by companies like Carbon Rotec.
We do not recommend to repair carbon spar caps with non-tolerable waves. That is why ACT recommends robust manufacturing processes and well train engineers and shop floor workers.
What are the advantages and disadvantages in usage of pultruded profiles or carbon-fabrics for theproduction of carbon-girders?
The design driver for long and slender blades are the bending stiffness to assure tower clearance and proper eigenfrequencies, as well as reduction of mass and edgewise mass moment of the blade. With the carbon fiber girder, these design goals can be achieved.
From a technical point of view, it is better to use pultruded carbon plates because they are prefabricated and have a high level of quality. But layup in a curved mould may not be very easy. We need machines to prepare the carbon plates and we shall consider some existing patents.
On the other hand, the achievable stiffness of infused carbon girders is about 20% less than the pultruded ones. Less stiffness can be compensated by additional carbon layers. The production process can be designed in a very robust way as well, and fewer machines and less production space are needed.